Processing of Lined PTFE Rubber Expansion Joints
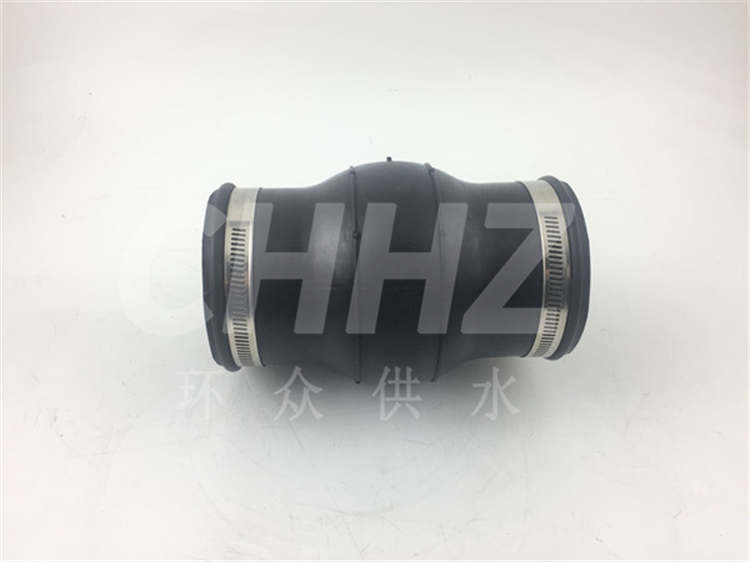
Introduction: Lined PTFE rubber expansion joints are critical components used in various industrial applications to accommodate movement, vibration, and misalignment while conveying a range of fluids. The manufacturing process of these expansion joints involves the integration of PTFE lining with rubber components, requiring specialized processing techniques and equipment. This article provides insights into the processing of lined PTFE rubber expansion joints, highlighting the key steps involved in their fabrication, the significance of each stage, and the quality considerations essential for ensuring reliable and durable products.
Preparation of Rubber Components: The processing of lined PTFE rubber expansion joints commences with the preparation of rubber components, primarily involving the cutting and shaping of rubber materials to the required dimensions. Superior-quality rubber compounds are selected based on their chemical and physical compatibility with the conveyed fluids and environmental conditions. The precision cutting of rubber layers is crucial for achieving accurate dimensions that will facilitate effective bonding with the PTFE lining, thereby ensuring structural integrity and performance.
Application of PTFE Lining: The application of PTFE lining to the prepared rubber components is a critical stage in the fabrication process. This step involves the adherence of PTFE material to the interior surfaces of the rubber expansion joint, creating a non-reactive, corrosion-resistant barrier for the conveyed fluids. The bonding process requires specialized adhesion techniques, such as heat and pressure application, to achieve a strong and durable bond between the PTFE lining and rubber substrate. Attention to uniform thickness and absence of defects in the lining application is essential for maintaining the desired chemical resistance and performance characteristics.
Molding and Vulcanization: After the application of PTFE lining, the rubber expansion joints undergo molding and vulcanization processes. Molding involves the shaping of the assembly to its final design, ensuring the formation of bellows and other structural features required for flexibility and expansion. Vulcanization, a heat and pressure-based curing process, serves to cross-link the rubber material, enhancing its mechanical properties and overall durability. This step is crucial for achieving optimal strength, resilience, and resistance to environmental factors and operational stresses, thereby ensuring the longevity and reliability of the expansion joints.
Quality Control and Testing: Throughout the processing of lined PTFE rubber expansion joints, stringent quality control measures are imperative to ensure adherence to performance standards and specifications. Non-destructive and destructive testing methods are employed to assess the integrity of the PTFE lining, bond strength, dimensional accuracy, and mechanical properties of the finished expansion joints. These evaluations are essential for validating the quality and reliability of the products, establishing their suitability for demanding industrial applications, and ensuring compliance with industry standards and regulations.
Conclusion: The processing of lined PTFE rubber expansion joints involves a series of meticulous and specialized steps aimed at integrating PTFE lining with rubber components to create robust, chemically resistant, and flexible expansion joints. From the precise preparation of rubber materials to the application of PTFE lining, molding, vulcanization, and comprehensive quality control, each stage contributes to the production of high-performance expansion joints tailored to the demands of diverse industrial environments. The successful execution of the processing steps is instrumental in delivering expansion joints that withstand operational challenges, provide reliable fluid conveyance, and contribute to the overall safety and efficiency of industrial systems.
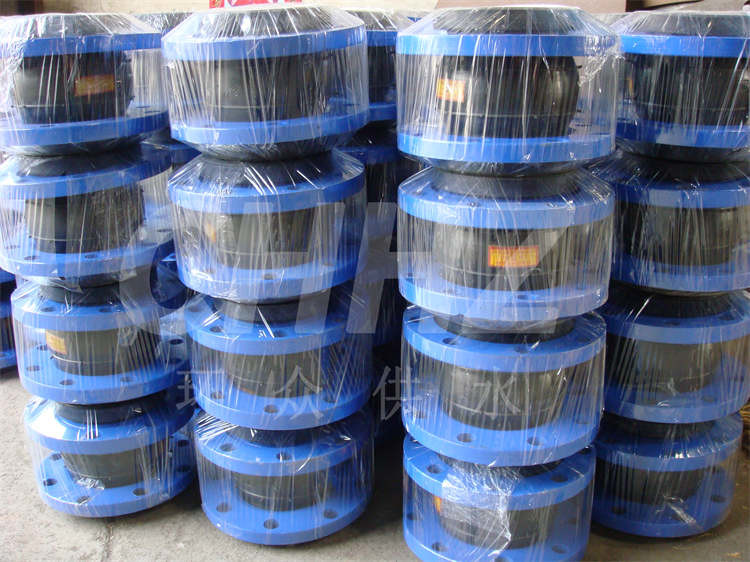