Rubber Hose Joint Processing - An Overview
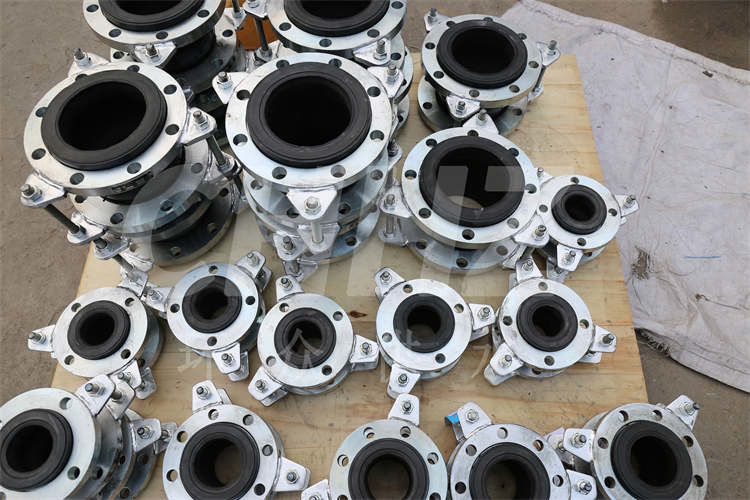
Introduction: Rubber hose joints play a crucial role in various industries, enabling flexible and reliable fluid transfer systems. To produce high-quality rubber hose joints, a meticulous fabrication process is essential. This article outlines the key steps involved in the processing of rubber hose joints, providing insights into the manufacturing techniques and quality considerations necessary for ensuring the functionality and durability of these essential components.
Material Selection and Preparation: The processing of rubber hose joints begins with the careful selection of elastomeric compounds, tailored to meet the specific requirements of the intended application. These compounds are then prepared through mixing, shaping, and extrusion to form the rubber components of the hose joints. Critical factors, such as chemical compatibility, tensile strength, and flexibility, are considered during material selection to ensure optimal performance and longevity of the finished product.
Fabrication of Reinforcement Layers: In applications that demand high-pressure resistance, fabric or metal wire reinforcement layers are incorporated into the rubber hose joints. This involves the precise positioning and integration of reinforcement materials during the fabrication process to impart the necessary structural integrity and pressure resistance. Adhering to specific design requirements and quality standards ensures the reliable performance of the hose joints under demanding operational conditions.
Molding and Vulcanization: The next step in processing rubber hose joints involves molding, which shapes the rubber compounds and reinforcements into the desired form. This stage ensures the creation of bellows, convoluted shapes, or other features essential for flexibility and movement. Subsequently, vulcanization, a curing process incorporating heat and pressure, is employed to cross-link the rubber molecules, enhancing their mechanical properties, durability, and resistance to environmental factors and operational stresses. Effective molding and vulcanization are critical in ensuring the overall performance and longevity of the rubber hose joints.
End Fitting Assembly: Following the molding and vulcanization processes, the incorporation of end fittings, such as flanges, couplings, or other connectors, is carried out. These end fittings are carefully selected based on the application requirements and are securely integrated into the hose joints to facilitate easy connection to the fluid transfer systems. Precision and attention to detail during this assembly stage are vital for achieving leak-free and reliable connections, contributing to the overall effectiveness of the finished rubber hose joints.
Quality Control and Testing: Throughout the fabrication process, stringent quality control measures are paramount to verify the integrity, dimensional accuracy, and performance attributes of the rubber hose joints. Non-destructive and destructive testing methods, including pressure testing, visual inspection, and material property evaluations, are employed to ensure that the finished products conform to industry standards and customer specifications. Comprehensive quality assessments validate the reliability and safety of the hose joints for their intended applications.
Conclusion: The processing of rubber hose joints is a multi-step procedure that demands precision, expertise, and adherence to stringent quality standards. From material selection and preparation to reinforcement integration, molding, vulcanization, end fitting assembly, and rigorous quality control, each stage contributes to the production of durable, reliable, and high-performance hose joints. Through meticulous processing and quality assurance, rubber hose joints can fulfill the essential role of facilitating efficient and safe fluid transfer across diverse industrial applications.
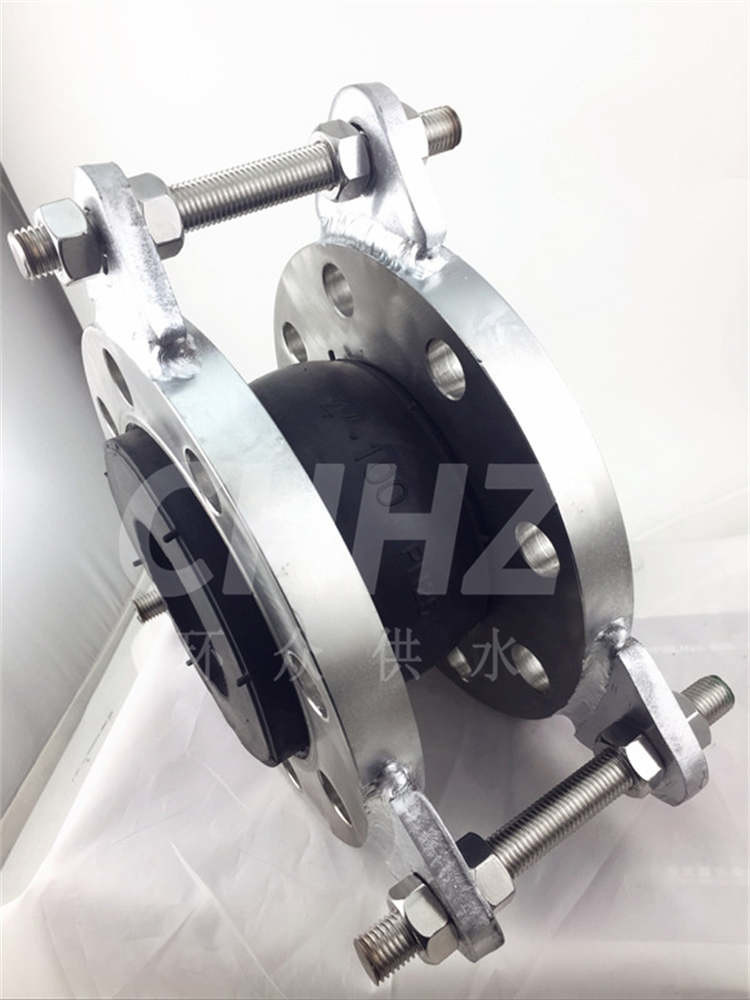