The design of rubber joints
Rubber joints, also known as rubber expansion joints, play a crucial role in modern piping systems by providing flexibility, vibration isolation, and stress relief. This article aims to explore the technical aspects of rubber joint technology, highlighting their design, functionality, and various applications in industrial and commercial settings.
The design of rubber joints is a culmination of meticulous engineering to ensure optimal performance under dynamic conditions. These components typically consist of a flexible rubber body with integrated reinforcing materials such as nylon or polyester cords, encapsulated within flanged or threaded end connections. The rubber material is often chosen for its resilience, flexibility, and ability to withstand a wide range of operating conditions, including temperature variations and chemical exposures.
Functionally, rubber joints serve to absorb movements and vibrations within piping systems, thereby reducing stress on adjacent components and preventing damage from occurring. They accommodate axial, lateral, and angular movements, as well as provide thermal expansion compensation, making them indispensable for applications where rigid connections are impractical or unsuitable. Additionally, rubber joints contribute to noise dampening and can mitigate the transmission of vibrations, enhancing overall system integrity and operational efficiency.
In industrial settings, rubber joints find extensive use in diverse applications such as HVAC systems, water treatment facilities, power plants, and chemical processing plants. Their ability to handle thermal expansion, dampen vibrations, and compensate for misalignment makes them ideal for these demanding environments. In commercial construction, rubber joints are utilized in piping systems for buildings, bridges, and infrastructure projects to ensure long-term durability and structural integrity.
The installation and maintenance of rubber joints are integral to their effective operation. Proper alignment, anchoring, and support are essential for maximizing their performance and longevity. Regular inspection for signs of wear, such as cracking, bulging, or degradation of the rubber material, is crucial to identify potential issues and initiate timely replacements or repairs. Additionally, ensuring chemical compatibility and addressing operational challenges such as pressure differentials are essential considerations for maintaining the reliability of rubber joints.
In conclusion, the technical intricacies of rubber joints underscore their significance in modern engineering and construction practices. Their versatile design, functional capabilities, and broad applicability make them indispensable components in piping systems across various industries. By understanding the technical nuances of rubber joint technology and adhering to best practices in their installation and maintenance, engineers and operators can harness the full potential of these critical elements to ensure safe and efficient operation of piping systems.
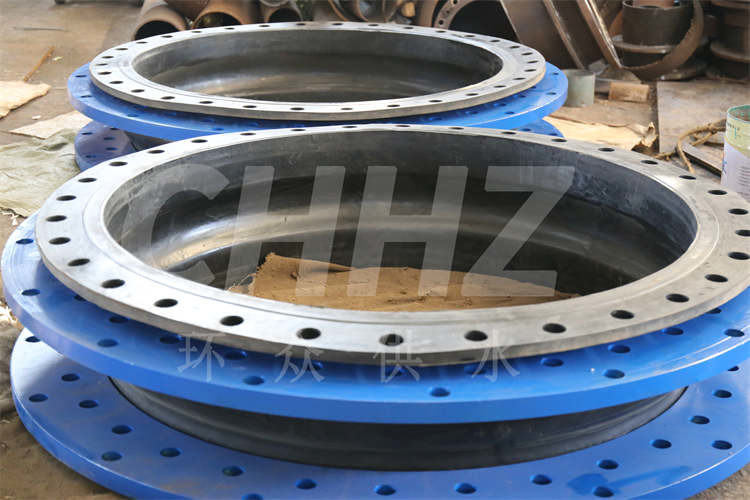