One of the primary reasons for rubber expansion joint
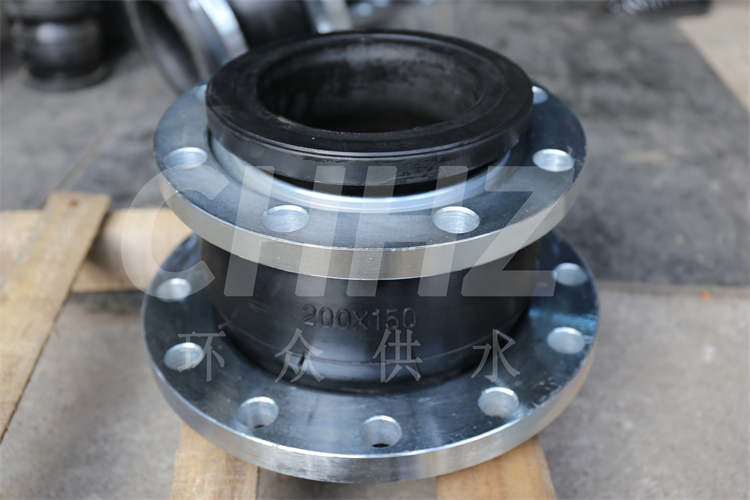
Rubber expansion joints are designed to provide flexibility and movement in piping systems, but like any mechanical component, they are susceptible to leaks if not properly installed or maintained. This article aims to address the issue of rubber expansion joint leaks, highlighting the potential causes and offering solutions to mitigate this common problem.
One of the primary reasons for rubber expansion joint leaks is improper installation. Inadequate alignment, incorrect torque application, or incorrect gasket placement can lead to compromised seals, resulting in leaks. Therefore, it is crucial to follow manufacturer's guidelines and best practices during installation to ensure proper sealing and prevent leakage.
Another common cause of rubber expansion joint leaks is mechanical wear and tear. Over time, the rubber material may degrade due to exposure to harsh chemicals, high temperatures, or excessive vibration, leading to cracks or deterioration of the joint. Regular inspection and preventive maintenance can help identify signs of wear and deterioration, allowing for timely replacement or repair to prevent leaks from occurring.
Furthermore, excessive movement, especially beyond the designed range of motion, can cause stress on the rubber joint, leading to deformation or damage to the sealing surfaces. It is essential to ensure that the piping system is properly supported, and movement is within the allowable limits as specified by the manufacturer to prevent overextension of the rubber expansion joint.
Leaks can also occur due to system overpressure, causing the joint to exceed its designed capacity and compromise the integrity of the seal. Implementing pressure relief valves and monitoring systems to prevent excessive pressure buildup is crucial for protecting the rubber expansion joint from damage and potential leaks.
Additionally, environmental or external factors such as excessive UV exposure, weathering, or physical damage can also contribute to rubber expansion joint leaks. Proper insulation, protective covers, and regular inspection can help mitigate these external influences and safeguard the integrity of the joint.
Addressing rubber expansion joint leaks requires a proactive approach that includes regular inspection, adherence to installation guidelines, preventive maintenance, and prompt replacement or repair as needed. By implementing these measures, operators and maintenance personnel can minimize the risk of leaks and ensure the reliable performance of rubber expansion joints in piping systems.
In conclusion, understanding the potential causes of rubber expansion joint leaks and implementing preventive measures is paramount to maintaining the integrity and reliability of piping systems. By adhering to best practices in installation, maintenance, and system operation, operators can mitigate the risk of leaks and ensure the effective performance of rubber expansion joints in their intended applications.
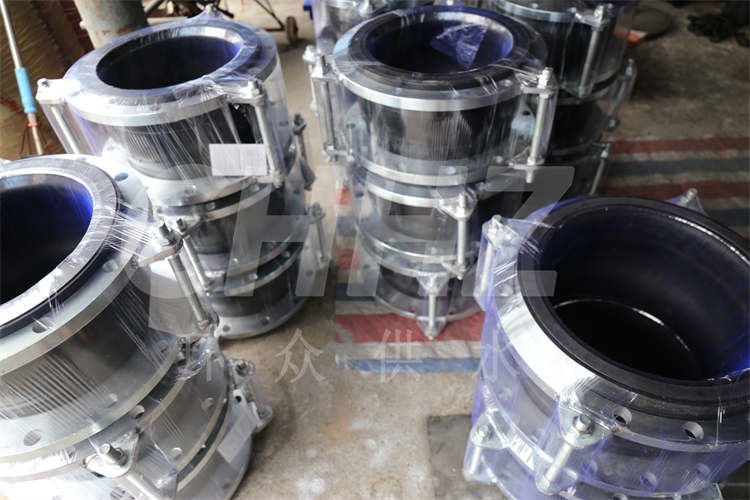