Rubber square joints
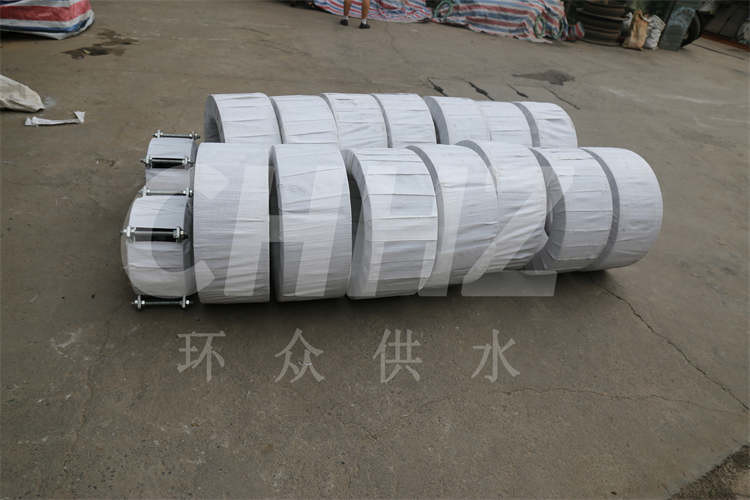
Rubber square joints, also known as rubber square expansion joints, are essential components used in various industrial applications to absorb movement, dampen vibrations, and compensate for misalignments in structures or piping systems. These joints are designed to provide flexibility and stability, particularly in situations where thermal expansion, contraction, or other dynamic forces occur.
The materials used in the construction of rubber square joints are carefully selected to ensure durability, resilience, and resistance to environmental factors. Commonly used materials include natural rubber and synthetic rubbers like EPDM (Ethylene Propylene Diene Monomer) or NBR (Nitrile Butadiene Rubber). Additionally, reinforcement materials such as fabric or metal inserts are often incorporated to enhance the structural integrity of the joints.
Rubber square joints are manufactured through a process that involves blending the selected raw materials, forming them into the desired square shape, and subjecting them to vulcanization, a process that imparts strength and elasticity to the rubber through heat and the addition of vulcanizing agents like sulfur.
The square shape of these joints allows them to accommodate movement in multiple directions, making them suitable for a wide range of applications where square or rectangular connections are required. They are widely utilized in the construction of infrastructure, industrial pipelines, HVAC systems, and machinery where they help to reduce stress at connection points and prevent damage due to movement and vibrations.
Proper installation and maintenance of rubber square joints are crucial for ensuring their long-term performance and reliability. Regular inspections should be conducted to check for signs of wear, degradation, or damage, and replacement or repair should be carried out as needed to prevent potential failures.
In conclusion, rubber square joints play a vital role in providing flexibility, stability, and durability in various industrial and mechanical applications. By selecting appropriate materials, designing for specific requirements, and ensuring proper installation and maintenance, these joints contribute to the efficient and reliable operation of systems while minimizing the risk of structural damage or leakage.
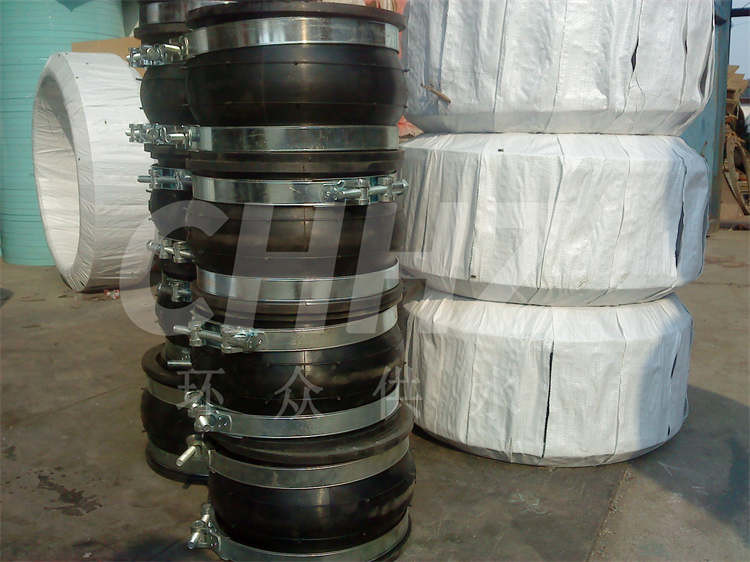