Rubber Joint Selection
When it comes to choosing rubber joints for industrial applications, several factors must be carefully considered to ensure optimal performance and longevity. The selection of appropriate rubber joints can significantly impact the efficiency and safety of piping systems, machinery, and other interconnected components. In this article, we will explore key considerations for selecting rubber joints and their impact on various industrial applications.
1. Media and Environmental Conditions:One of the primary considerations when choosing rubber joints is the nature of the media (liquids, gases, or solids) being transported through the piping system. Different rubber compounds are designed to withstand specific chemicals, temperatures, and pressures. Therefore, it is essential to evaluate the compatibility of the rubber material with the media to prevent corrosion, degradation, or failure.
Additionally, environmental factors such as temperature variations, UV exposure, ozone, and weathering should be taken into account when selecting rubber joints. Environmental resistance properties of the rubber material must align with the operating conditions to ensure long-term reliability.
2. Movement and Vibration:Rubber joints are commonly used to absorb movement, vibration, and noise in piping systems and machinery. The selection of rubber joints should account for the anticipated movement, including axial, lateral, and angular displacement, as well as the frequency and amplitude of vibrations. Understanding the dynamic forces within the system will help in choosing rubber joints with appropriate flexibility, stiffness, and damping characteristics.
3. Pressure and Flow Rate:The operating pressure and flow rates within the piping system are crucial factors in selecting rubber joints. Proper consideration of these parameters is essential to prevent over-compression, blowouts, or restrictions in flow. The design of the rubber joints should accommodate the expected system pressures and fluid velocities while maintaining structural integrity and sealing properties.
4. Installation and Maintenance:Ease of installation, accessibility for maintenance, and the lifespan of rubber joints should also be factored into the selection process. Choosing rubber joints that are compatible with the installation method and can be easily inspected and replaced when necessary will contribute to the overall efficiency and cost-effectiveness of the system.
In conclusion, the selection of rubber joints plays a critical role in the performance, safety, and longevity of industrial systems. By considering factors such as media compatibility, environmental conditions, movement and vibration requirements, pressure and flow rates, as well as installation and maintenance aspects, engineers and operators can make informed decisions that lead to reliable and efficient operation. Prioritizing the selection of high-quality rubber joints tailored to specific application requirements is essential for ensuring the overall integrity and functionality of industrial systems.
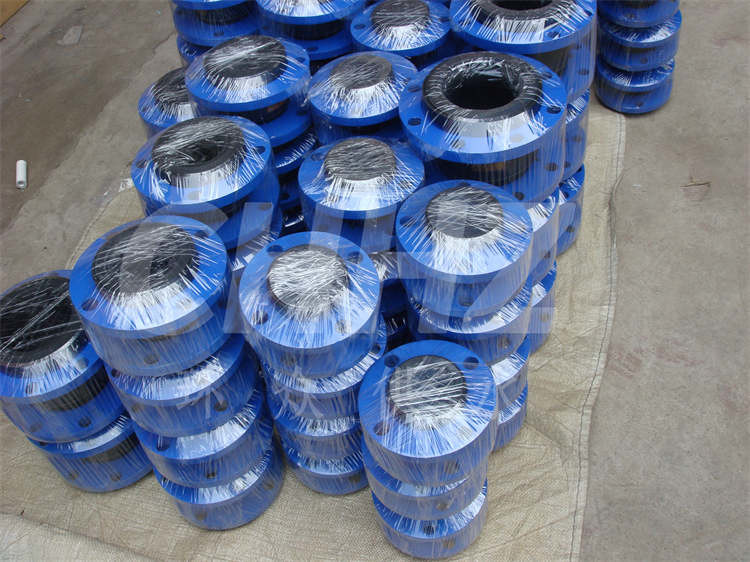