Nitrile (NBR) Rubber Joints vs. EPDM Rubber Joints
Nitrile (NBR) rubber joints and EPDM rubber joints are two widely used types of rubber joints in various mechanical and industrial applications. Both materials offer unique properties and advantages, and understanding their differences and applications is crucial for proper selection and installation. This article provides an overview of the characteristics, applications, and considerations associated with nitrile rubber joints and EPDM rubber joints.
Nitrile (NBR) Rubber Joints:Nitrile rubber, commonly known as NBR, is a synthetic rubber with high resistance to oil, fuel, and other hydrocarbons. NBR rubber joints are characterized by their excellent compatibility with petroleum-based fluids and resistance to abrasion, making them suitable for applications involving oils, lubricants, and hydraulic fluids. These joints exhibit good mechanical properties and a wide temperature tolerance range, allowing them to withstand challenging operating conditions. Nitrile rubber joints are commonly used in hydraulic systems, automotive components, and machinery where exposure to oil and fuel is prevalent.
EPDM Rubber Joints:Ethylene Propylene Diene Monomer (EPDM) rubber joints are known for their exceptional resistance to weathering, ozone, and ultraviolet exposure. EPDM rubber exhibits superior thermal stability and excellent electrical insulation properties, making it an ideal choice for outdoor and weather-exposed applications. EPDM rubber joints are commonly used in roofing systems, outdoor piping, sealing applications, and automotive components due to their resistance to weathering, water, and steam. The material's durability and flexibility make it suitable for extended outdoor use and exposure to harsh environmental conditions.
Application Considerations:When selecting between nitrile rubber joints and EPDM rubber joints, it's essential to consider the specific operating environment, fluid compatibility, temperature range, and mechanical requirements. Nitrile rubber is preferred for applications involving contact with oils, fuels, and hydraulic fluids, whereas EPDM rubber excels in outdoor, weather-exposed applications where resistance to UV, ozone, and weathering is critical. Proper installation, including ensuring correct sizing, adequate support, and appropriate anchoring, is vital to ensure the optimal performance and longevity of both types of rubber joints.
In conclusion, nitrile rubber joints and EPDM rubber joints offer distinct advantages and are tailored for specific applications based on their inherent properties. By understanding the unique characteristics of each material and considering the requirements of the intended application, stakeholders can make informed decisions when selecting and installing rubber joints to ensure efficient and reliable performance in their respective systems.
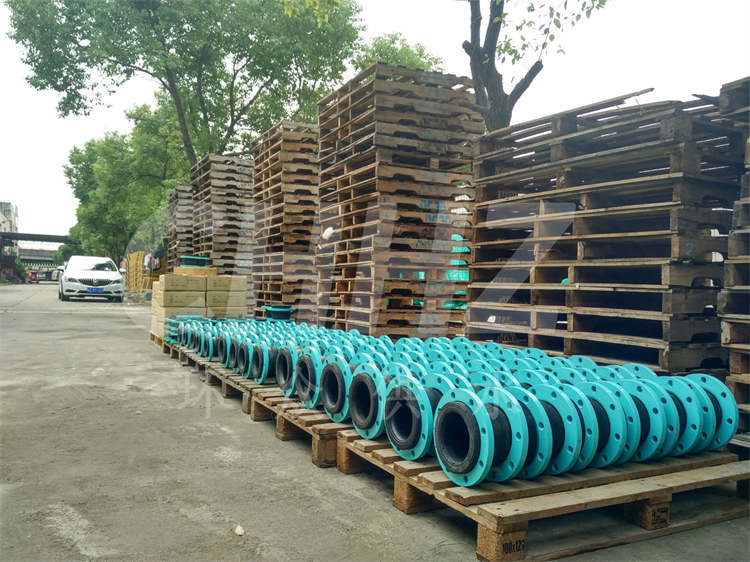