Acid and Alkali Resistant Rubber Expansion Joints
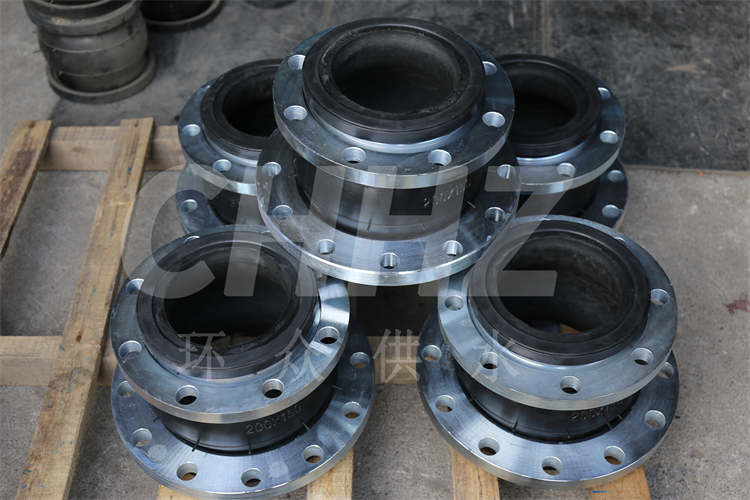
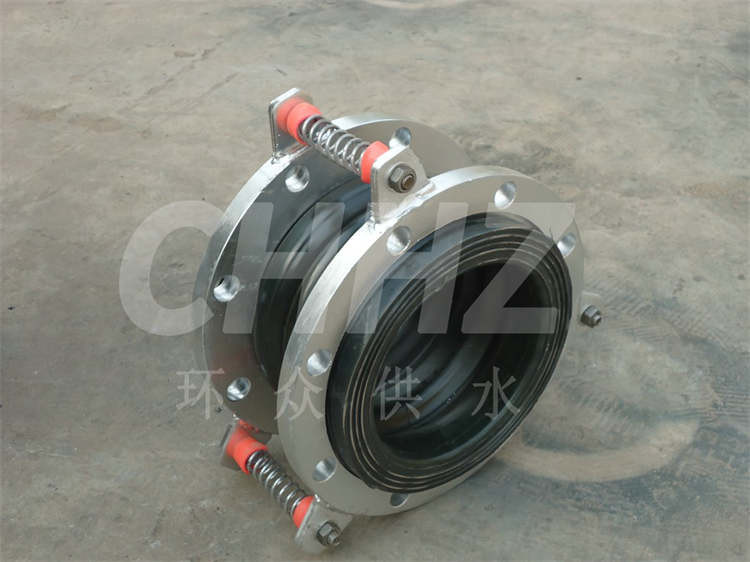
Acid and alkali resistant rubber expansion joints are critical components used in various industrial and chemical processing applications to accommodate movement, absorb vibration, and withstand the corrosive effects of acidic and alkaline environments. This article aims to provide insight into the characteristics, applications, and considerations associated with acid and alkali resistant rubber expansion joints.
Characteristics:The primary characteristic of acid and alkali resistant rubber expansion joints is their ability to withstand the corrosive effects of acidic and alkaline substances. These joints are typically manufactured using high-quality synthetic rubber compounds, such as EPDM (Ethylene Propylene Diene Monomer) or FKM (fluoroelastomer), that exhibit exceptional chemical resistance. Additionally, these joints feature reinforced construction and flanged ends to provide flexibility, absorb movement and vibrations, and maintain a tight seal under challenging conditions. The materials used ensure resistance to a wide range of chemicals, including strong acids, bases, and oxidizing agents, making them suitable for various industrial processes and chemical handling systems.
Applications:Acid and alkali resistant rubber expansion joints find application in diverse industries, including chemical processing, petrochemical, pharmaceutical, wastewater treatment, and industrial manufacturing. These joints are used in piping systems, ductwork, and equipment where exposure to corrosive chemicals, temperature fluctuations, and mechanical stress is prevalent. Their ability to accommodate movement and vibration while maintaining a tight seal makes them essential components in systems where reliable and durable performance is paramount. Acid and alkali resistant rubber expansion joints play a vital role in minimizing the risk of leaks, system downtime, and equipment damage associated with chemical exposure and environmental factors.
Considerations:When specifying and installing acid and alkali resistant rubber expansion joints, several considerations are crucial to ensure their optimal performance. In addition to selecting the appropriate material based on the specific chemical exposure, factors such as temperature range, pressure ratings, movement capability, and installation guidelines must be carefully evaluated. Proper installation, including correct sizing, anchoring, and maintenance, is essential to maximize the service life and effectiveness of acid and alkali resistant rubber expansion joints in demanding applications.
In conclusion, acid and alkali resistant rubber expansion joints are indispensable components in industries where corrosive chemicals and environmental factors can compromise the integrity of piping systems and equipment. Understanding the unique properties of these joints and adhering to proper selection, installation, and maintenance practices can help mitigate potential risks and ensure reliable performance in the challenging conditions they are designed to withstand.
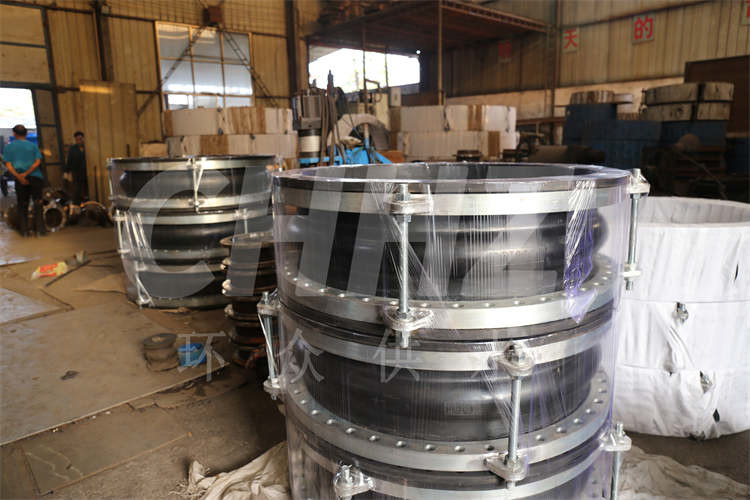