The Differences Between PTFE Rubber Joints and Ordinary Rubber Joints
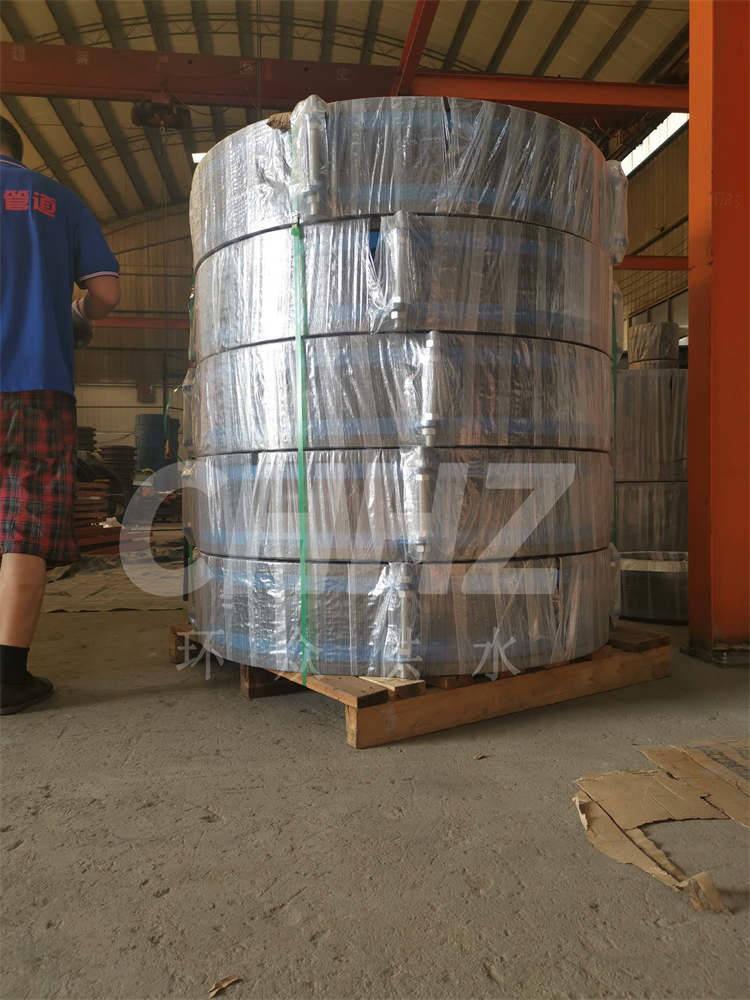
PTFE (polytetrafluoroethylene) rubber joints and ordinary rubber joints serve critical roles in piping systems, offering different properties and performance characteristics. This article aims to elucidate the distinctions between these two types of rubber joints, highlighting the unique features, applications, and considerations associated with each.
Material Composition:The primary difference between PTFE rubber joints and ordinary rubber joints lies in the material composition. PTFE rubber joints are manufactured using a rubber compound infused with PTFE, a synthetic fluoropolymer known for its exceptional chemical resistance and low coefficient of friction. In contrast, ordinary rubber joints are typically composed of natural rubber or synthetic rubbers such as EPDM or Nitrile. The incorporation of PTFE in the rubber matrix imparts superior resistance to aggressive chemicals, high temperatures, and extreme environmental conditions to PTFE rubber joints, making them ideal for demanding industrial applications.
Chemical Resistance:PTFE rubber joints exhibit outstanding resistance to a wide range of chemicals, including strong acids, bases, solvents, and corrosive substances that can degrade conventional rubber materials. The inert nature of PTFE provides a barrier against chemical attack, ensuring the integrity and longevity of the joint in aggressive chemical environments. In contrast, while ordinary rubber joints offer good resistance to general-purpose fluids and moderate chemical exposure, they may not be suitable for applications involving highly corrosive substances or elevated temperatures.
Temperature and Pressure Ratings:Another notable difference between PTFE rubber joints and ordinary rubber joints is their temperature and pressure capabilities. PTFE rubber joints can withstand a broader temperature range and higher pressures compared to ordinary rubber joints. The inherent thermal stability and mechanical strength of PTFE contribute to its ability to operate effectively at extreme temperatures and pressures, making PTFE rubber joints suitable for applications where temperature differentials and fluctuating pressures are prevalent.
Applications:Due to their exceptional chemical resistance and high-temperature performance, PTFE rubber joints are commonly used in industries such as chemical processing, petrochemical, pharmaceutical, and food processing, where exposure to aggressive chemicals and elevated temperatures is a concern. Ordinary rubber joints, on the other hand, find widespread use in water supply, HVAC systems, and general industrial applications where the operating conditions are relatively benign and do not require the specialized chemical resistance and thermal properties of PTFE rubber joints.
In conclusion, the distinctions between PTFE rubber joints and ordinary rubber joints are rooted in their material composition, chemical resistance, temperature and pressure ratings, and applications. Understanding these differences is essential for selecting the appropriate type of rubber joint tailored to the specific requirements of a given application, ensuring reliable performance and long-term integrity in diverse operating conditions.
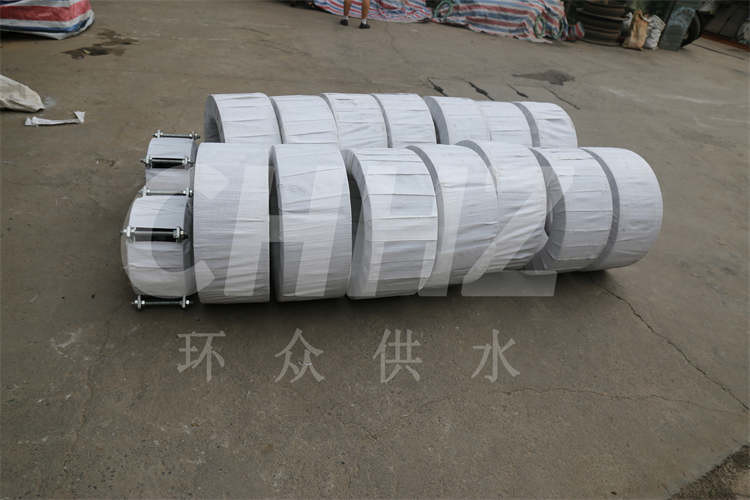