The influence of corrugated expansion joint forming method on service life
There are many different methods used to form corrugated expansion joints, but the following three methods are suitable for the corrugated expansion joints for heating:
Expansion mold forming: The mold expands inside the barrel embryo and expands to form corrugations one by one. Then, the inner and outer rollers of the standard corrugated profile line are used for fine pressing and shaping.
Hydroforming: The die is set in groups on the outside of the barrel embryo, liquid is injected into the inside of the barrel embryo, pressure is applied until the barrel embryo material yields, pressure is maintained and the die is lowered together with the die until the correct waveform is obtained, generally for one-time overall forming.
Roll Forming: A forming wheel is provided inside and outside the barrel, and the barrel or forming wheel is rotated. At the same time, the forming wheel is pressurized and the longitudinal shrinkage of the barrel is controlled until the correct waveform is obtained. Generally, wave by wave forming.
The difference between these three methods is that the cold work hardening of the corrugated expansion joint during the forming process is different. The cold work hardening of the wave valley part is higher than the wave peak part in the hydraulic forming, and the wave peak part will be subjected to larger displacement when working. The cold hardening of the peaks and valleys of the other two methods is basically the same, and can withstand the same displacement, but the corrugated expansion joints of roll forming will leave a larger residual stress, and some corrugated expansion joints even crack during the forming process, so generally after forming to do heat treatment.
Cold hardening will cause residual stresses in the corrugated expansion joints, but the cold hardening is not always a negative impact. For the austenitic stainless steel as the material of the bellows, the cold work hardening during processing can significantly improve the service life of the corrugated expansion joint, which has been confirmed by a large number of practice. However, because the degree of cold hardening is difficult to describe in a quantitative way, so which molding method in line with the results of the design formula, which molding method is beneficial and the service life of the product, is difficult to say. The corrugated expansion joint works with stresses in the plastic deformation zone of the material. Such large stresses can make the heat treatment done after forming meaningless in a very short time. In terms of the stresses generated by a 200-week product in operation, all the factors that contribute to the service life are cancelled out within a very short period of service. Moreover, no manufacturer can guarantee that its forming process will produce the proper cold work hardening of the bellows. Therefore, it is necessary to properly increase the design fatigue life of the product.
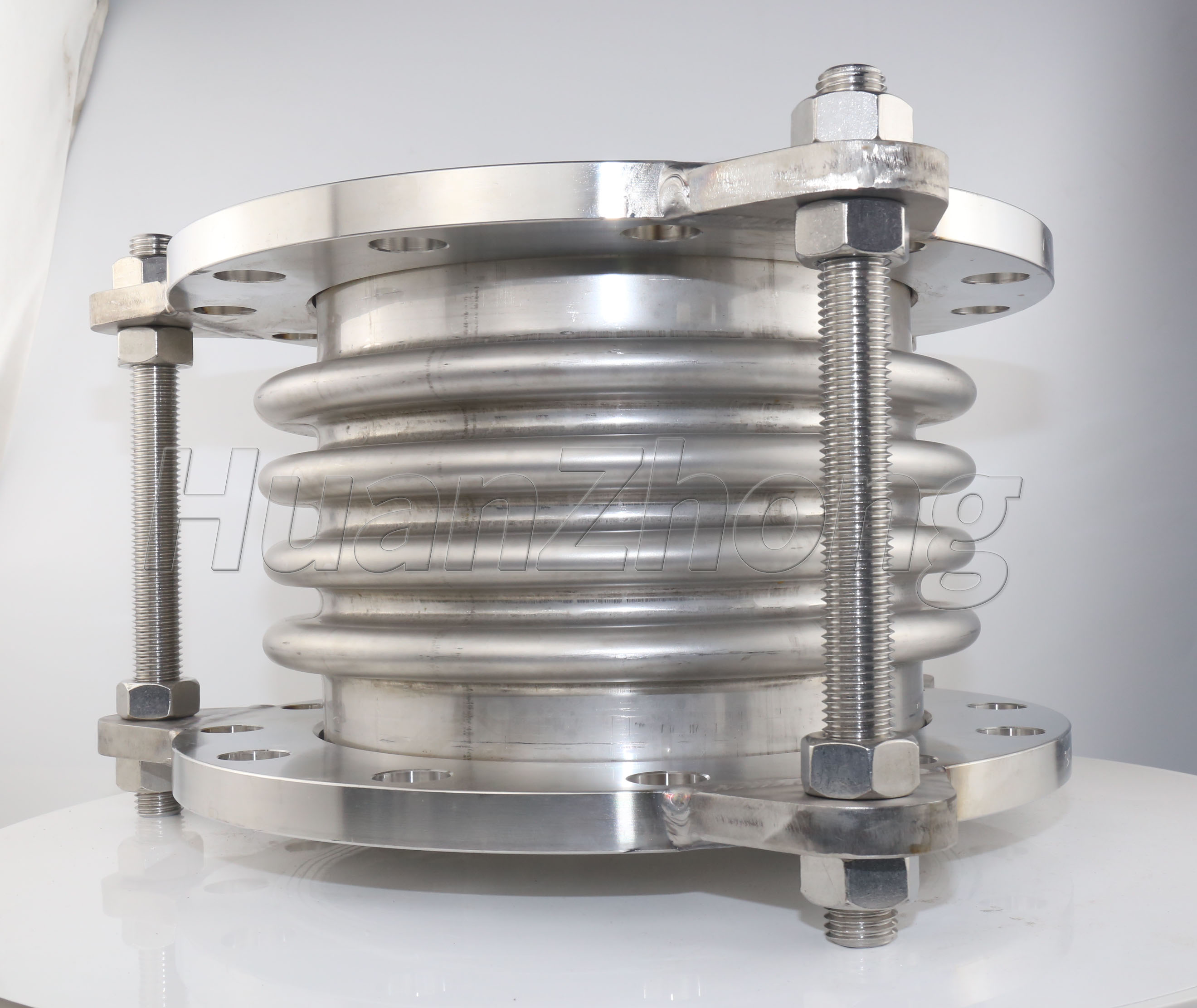