Manufacturing Process of Rubber Hose Fittings: A Comprehensive Overview
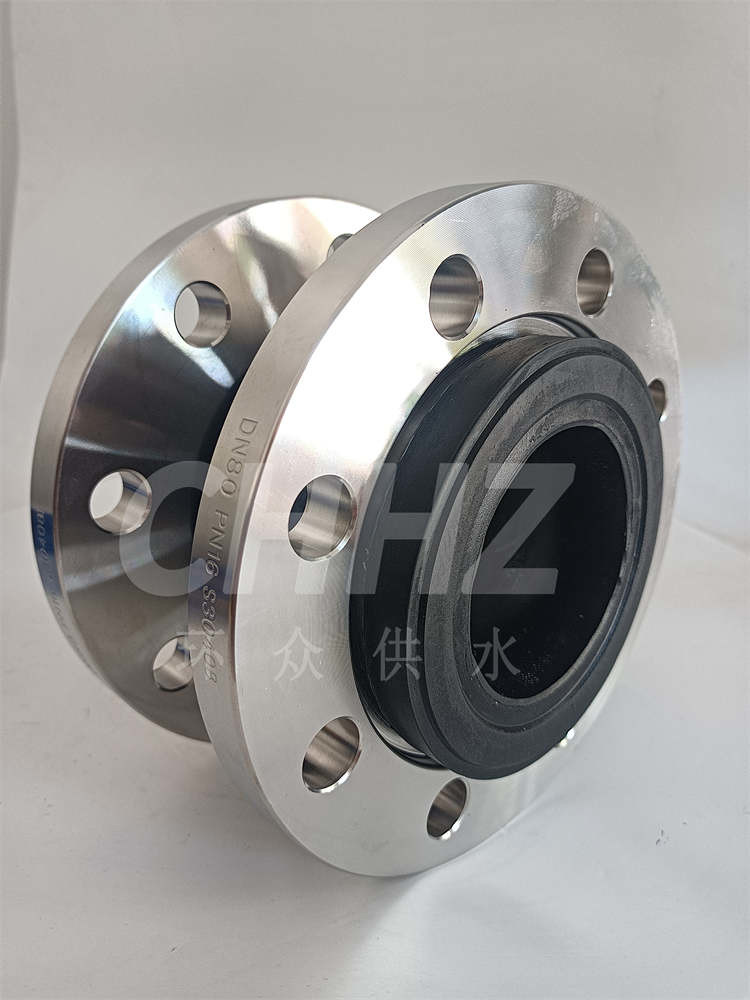
The production of high-quality rubber hose fittings involves a series of meticulous processes designed to ensure precision, durability, and performance. The following is a detailed description of the manufacturing process of rubber hose fittings, from material selection to the final quality checks.
Raw Material Selection:The manufacturing process begins with the careful selection of suitable raw materials. High-grade rubber compounds, such as EPDM, Nitrile, or silicone, are chosen based on the specific application requirements, considering factors such as temperature resistance, chemical compatibility, and flexibility. Similarly, for metal hose fittings, materials such as stainless steel, brass, or aluminum are chosen based on mechanical properties and environmental considerations.Extrusion of Rubber Hose:The selected rubber compound undergoes an extrusion process to form the rubber hose. During extrusion, the raw material is forced through a die of the desired cross-sectional shape to create continuous lengths of flexible rubber hoses. Precise control of temperature, pressure, and material consistency is essential to achieve uniformity and integrity in the extruded rubber hose.
Molding of Hose Fittings:Simultaneously, metal hose fittings are manufactured through precision molding processes. High-precision molds, often made from tool steel, are utilized to mold metal fittings into the desired shapes and dimensions. This process allows for the creation of intricate features, including threads, barbs, and sealing surfaces, ensuring compatibility with various hose types and applications.
Surface Treatment and Finish:Following the molding process, metal hose fittings may undergo surface treatment and finishing operations. This may include processes such as deburring, polishing, plating, or coating to enhance corrosion resistance, improve surface smoothness, or provide aesthetic appeal. Surface finish treatments are optimized to meet performance, appearance, and environmental requirements.
Assembly of Rubber Hose and FittingsThe assembled rubber hoses and metal fittings are brought together in a careful assembly process. Depending on the design, hoses may be manually or automatedly attached to fittings using compression, crimping, or other joining techniques. A secure and leak-free connection between the rubber hose and the fitting is paramount, necessitating great attention to detail during the assembly process.
Quality Control and Testing:Throughout the manufacturing process, rigorous quality control measures are in place to ensure that the rubber hose fittings meet specified standards. Dimensional accuracy, material composition, surface finish, and assembly integrity are thoroughly inspected. In addition, pressure and leakage tests are conducted to validate the performance and reliability of the assembled hose fittings.
Final Packaging and Shipment:Once the rubber hose fittings have passed quality inspection, they are packaged and prepared for shipment. Proper packaging techniques are employed to safeguard the components during transit and storage. Clear labeling and documentation ensure that product specifications and traceability information are readily accessible.
In conclusion, the careful and methodical manufacturing process of rubber hose fittings illustrates the precision and expertise required to produce components that meet demanding performance standards across a wide range of industries and applications. Adherence to stringent quality control standards, materials engineering principles, and advanced production techniques contributes to the reliability and longevity of rubber hose fittings in the field.
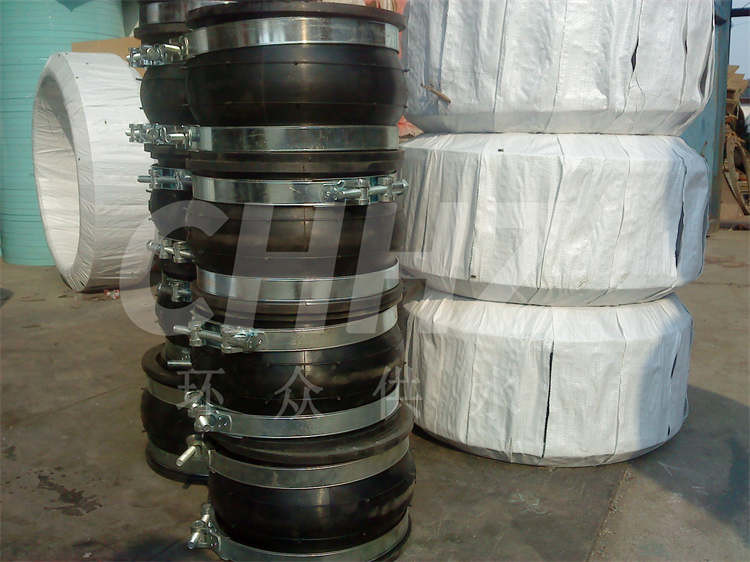