High Voltage Power Cable Joint Rubber: An Overview
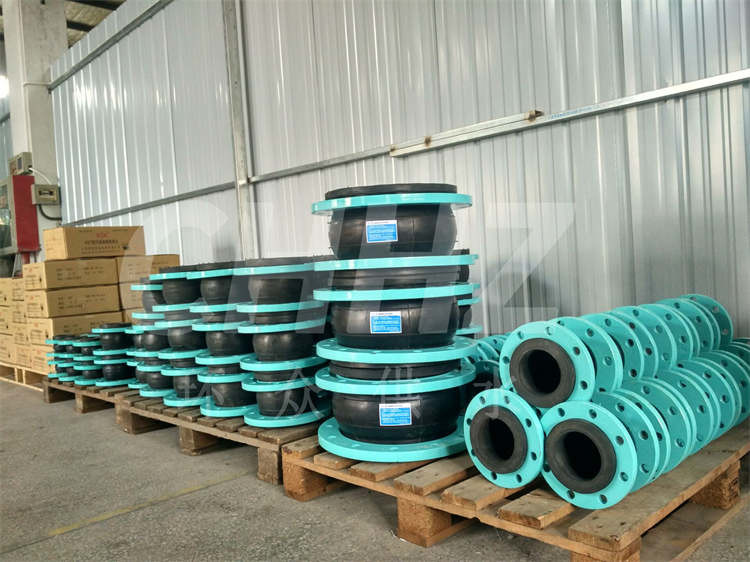
The production of high voltage power cable joint rubber is a critical aspect of ensuring the integrity and reliability of electrical power transmission systems. Here's an overview of the manufacturing process involved in creating robust and dependable cable joint rubber components.
Raw Material Selection:The initial phase of the manufacturing process involves the careful selection of raw materials. High-quality elastomers, such as ethylene propylene diene monomer (EPDM) or silicone rubber, are chosen for their exceptional electrical insulation properties, thermal stability, and resistance to environmental factors. Additionally, fillers and additives are meticulously selected to achieve the desired mechanical and electrical performance characteristics.
Formulation and Compounding:The selected rubber compounds undergo a precise blending and compounding process. This step involves the thorough mixing of the elastomers, fillers, curing agents, and other additives to create a homogenous, uniform compound. The compounding process is crucial in achieving the desired mechanical strength, flexibility, and electrical insulation properties necessary for high voltage cable joint rubber.
Extrusion and Molding:The compounded rubber is then processed through extrusion or molding techniques to produce cable joint components with the required cross-sectional profiles. Extrusion allows for the creation of continuous lengths of rubber profiles or sheaths, while molding enables the formation of intricate shapes and specialized components such as stress cones and connectors. Strict control over temperature, pressure, and curing parameters is crucial to ensure uniformity and dimensional accuracy.
Vulcanization and Curing:Once the rubber components are shaped, they undergo vulcanization and curing processes. Vulcanization involves the application of heat and pressure to the rubber compound, leading to cross-linking of polymer chains and the development of durable mechanical properties. Curing agents and curing cycles are tailored to achieve optimal electrical insulation, thermal resistance, and resilience in the finished cable joint rubber components.
Testing and Quality Control:Every stage of the manufacturing process is subject to stringent testing and quality control measures. Material properties, including electrical resistance, dielectric strength, and thermal stability, are carefully assessed to confirm compliance with industry standards and specifications. Non-destructive and destructive testing methods, such as dielectric testing and mechanical testing, are employed to validate the integrity and performance of the cable joint rubber components.
Packaging and Storage:Following successful quality validation, the cable joint rubber components are carefully packaged to protect them during transit and storage. Proper labeling and documentation ensure clear identification of product specifications and traceability information. Packaging materials are selected to safeguard the components from environmental factors and mechanical damage.
In summary, the manufacturing process of high voltage power cable joint rubber involves a combination of materials engineering, precision processing, and stringent quality control. The resulting components are designed to meet the demanding requirements of power distribution and transmission systems, providing reliable electrical insulation and mechanical protection in critical applications. Adherence to stringent manufacturing standards and expertise in rubber compounding and processing are instrumental in ensuring the performance and longevity of high voltage cable joint rubber components.
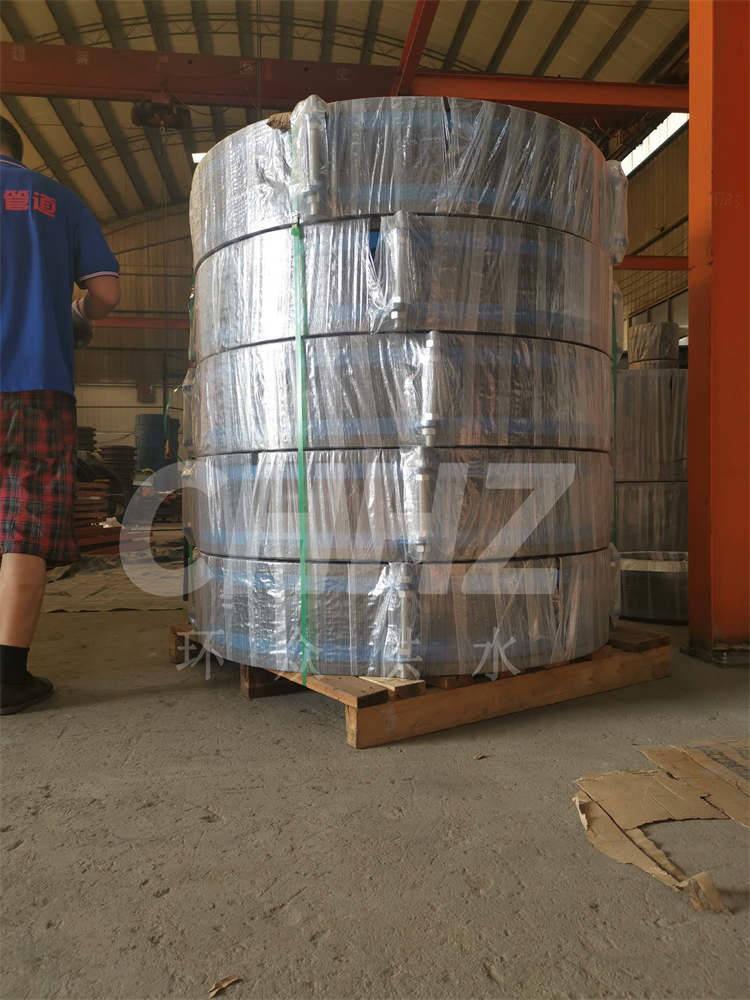