Mid-Joint for Rubber-Insulated Flat Cable with Steel Wire
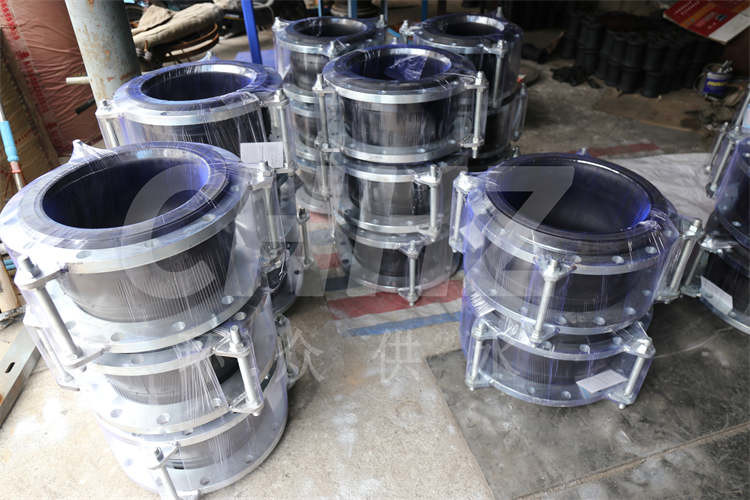
Introduction:Mid-joints for rubber-insulated flat cables with steel wire play a crucial role in electrical power transmission and distribution systems. This article provides an overview of the design, manufacturing, and installation of mid-joints, highlighting their importance in ensuring reliable and uninterrupted electricity supply.
Design Considerations:Mid-joints for rubber-insulated flat cables with steel wire are meticulously designed to accommodate the unique characteristics of these cables. The joint structure must provide secure electrical connectivity, mechanical strength, and effective insulation while accommodating the flat geometry and steel wire reinforcement. Additionally, the design accounts for environmental factors, ensuring resilience against moisture, temperature variations, and mechanical stress.
Materials and Components:High-quality materials are employed in the construction of mid-joints to ensure long-term performance and durability. The insulation materials are selected for their robust electrical properties, resistance to abrasion, and compatibility with rubber insulation. Connectors, clamps, and reinforcing elements are carefully chosen to provide reliable electrical connections and mechanical integrity.
Manufacturing Process:The production of mid-joints involves precision engineering and manufacturing processes. The rubber insulation is carefully shaped to match the configuration of the flat cable, incorporating grooves and contours to ensure a snug fit and effective sealing. Steel wire connectors are integrated to establish secure electrical contacts, and the assembly undergoes rigorous quality control checks to verify dimensional accuracy and material properties.
Installation and Sealing:During installation, meticulous attention is given to properly aligning the flat cable ends, ensuring that the steel wires are securely connected, and that the rubber insulation is effectively sealed. Various sealing techniques, including compression molding and heat-shrink tubing, are employed to protect the joint from moisture ingress and provide mechanical reinforcement.
Electrical Testing and Quality Assurance:Following the installation of mid-joints, comprehensive electrical testing is conducted to validate the integrity and performance of the connections. Insulation resistance, dielectric strength, and continuity tests are performed to confirm the joint's ability to withstand operational voltages and environmental conditions. Quality assurance protocols ensure that each mid-joint meets specified standards and is capable of withstanding the rigors of service life.
Applications and Benefits:Mid-joints for rubber-insulated flat cables with steel wire are extensively used in power distribution networks, substation connections, and industrial applications. Their robust design and reliable performance contribute to the safe and efficient operation of electrical systems, minimizing downtime and maintenance costs associated with cable joint failures.
In conclusion, mid-joints for rubber-insulated flat cables with steel wire form a critical link in the electrical power grid, providing secure and durable connections essential for uninterrupted power transmission. The meticulous design, quality manufacturing, and rigorous testing of these mid-joints ensure the resilience and longevity of cable installations, contributing to the reliability and safety of electrical infrastructure.
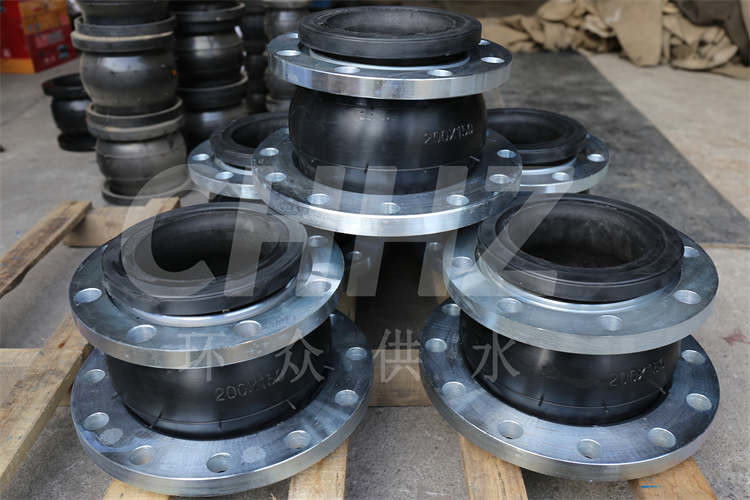